Light burned magnesium powder It is an important refractory. Light burned magnesia powder is a raw material with medium alkalinity and chemical activity. In addition to being used as refractory and cementitious material, it is also used in other industrial fields. In addition, the development of converter slag splashing technology has further expanded the application range of light burned magnesia powder. At present, slag splashing furnace protection technology mostly uses light burned magnesia powder to form balls, including light burned magnesia powder balls, carbon containing light burned magnesia sub balls and carbon containing calcium containing light burned magnesia powder balls. Light burned magnesia powder, referred to as light burned magnesia powder, is a kind of active magnesium oxide obtained by calcining magnesite, brucite and magnesium hydroxide extracted from seawater or brine at about 800~1000 ℃. Light burned magnesia powder is light yellow and light brown powder, the particle size is mostly below 100 mesh, the periclase crystal is very small, and the density of light burned magnesia powder
Light burned magnesium ball The preparation of is to add 80% light burned magnesium powder into 2O water, put it into a roller mixer for rolling, mixing, and mixing for 15~20 min to form a mixture, and then send it to the ball press through the belt conveyor to prepare the product, and then stack it. After 48h drying in the shade and forming strength, the finished light burned magnesium ball is ready for sale.
Improvement of light burned magnesium ball production process
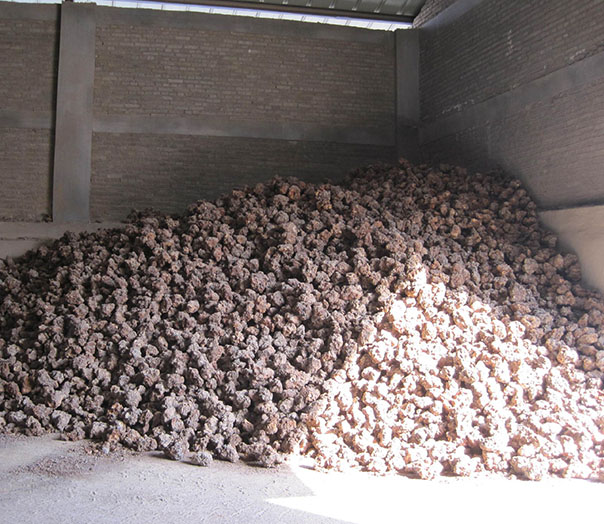
Necessity of improving the production process of light burned magnesium ball
After years of production practice, the light burned magnesium ball products are produced according to the above preparation process, and the product quality has the following problems.
1) The sphere is loose. Small density, low strength, easy to break. Especially in loading, unloading, transportation, extrusion and falling, the ball is easy to be broken.
2) Low balling rate. After the raw materials are processed by the ball press, half of them are products and half are powder particles. The powder particles need to be returned to the ball press manually
Further processing.
3) The user was not satisfied. The products sold contain 20% - 35% small particles, powder particles and other mixtures, which users have raised objections for many times.
4) The shape of the sphere is incomplete. Some are half balls, some are one-third balls, and some are missing corners, with different shapes and dull surfaces,
Poor appearance